Operations
Operations
Streamline & Scale: Smart Ops for Modern Founders
From systems that save you time to workflows that actually work, our operations column helps you run a lean, profitable business without the chaos. Discover automation tips, backend strategies, and process-driven insights designed for female entrepreneurs who want to work smarter—not harder.
Ready to grow your brand—your way?
Whether you need systemizing your business or streamlining automation, FemFounder is your home base.
→ [Get the Free PR Starter Kit] – land your first (or next) feature
→ [Work with Marquet Media] – high-impact PR & brand storytelling
→ [Shop Templates & Tools] – build faster with pro-level resources
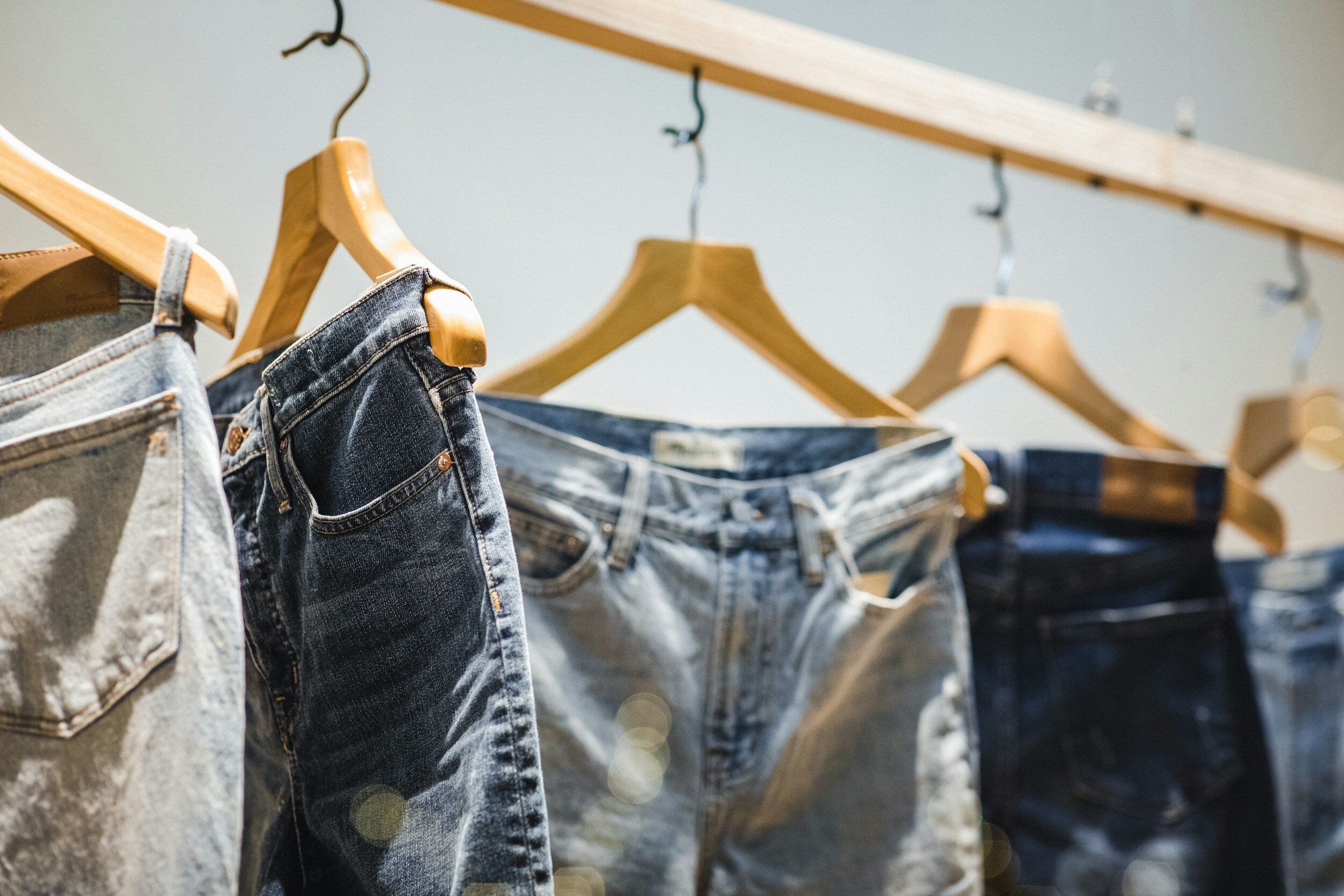
Enhancing Logistics and Operations in the Apparel Industry
In our current, swiftly moving business environment, getting things done swiftly and effectively holds paramount importance across all sectors of commerce, clothing businesses included. Handling stock levels and ensuring customer deliveries are made on time are essential for staying ahead in the game.
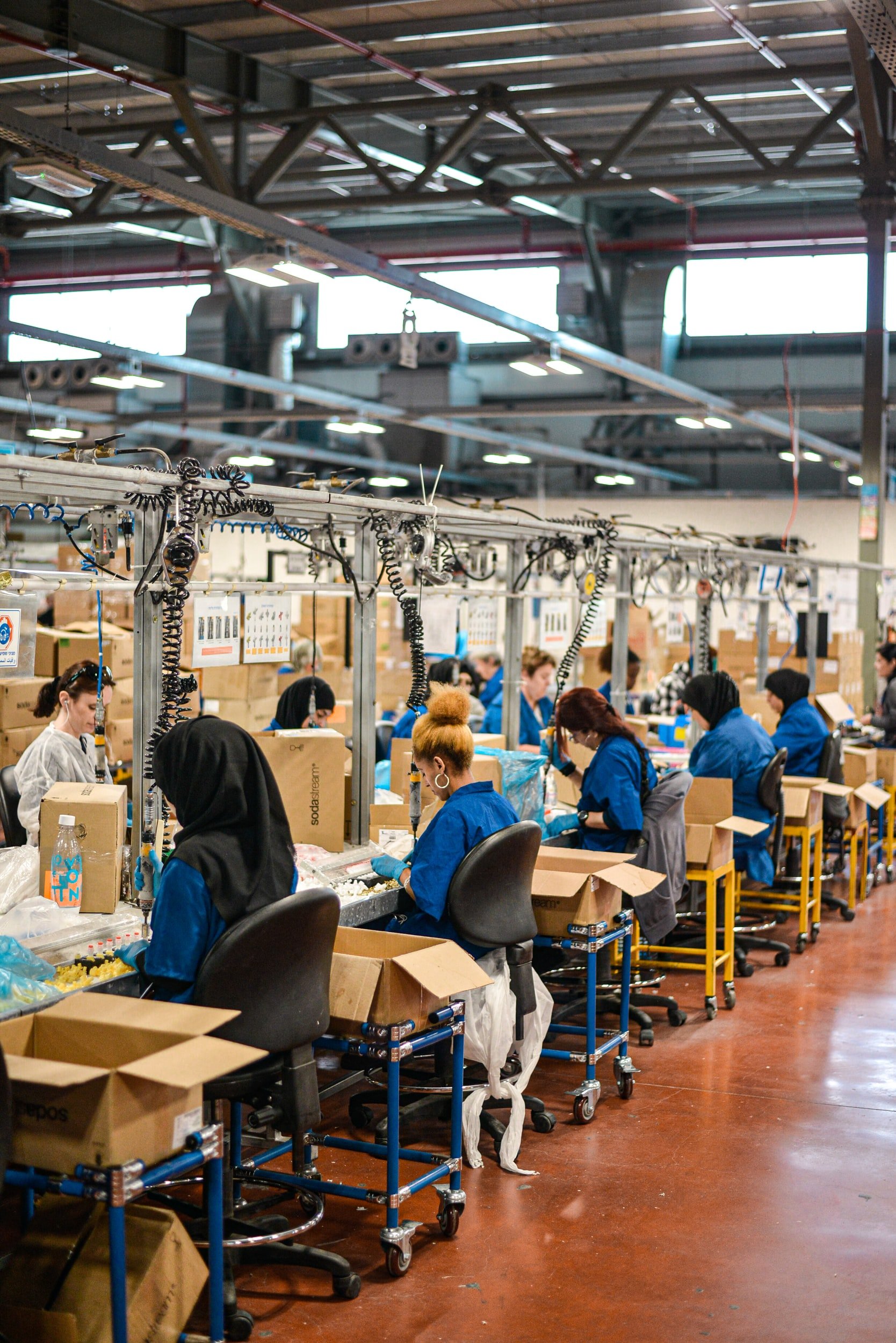
